リチウムイオン電池業界の変遷
1991年にソニー(当時はソニーエナジーテック社)が世界で初めてリチウムイオン電池の商品化に成功し、当時はカムコーダ(ハンディビデオカメラ)に搭載され爆発的にヒットとなった。90年代はソニーに続きATバッテリー(東芝と旭化成の合弁)、SANYO、Panasonicとリチウムイオン電池のリーディングカンパニーとして世界シェア90%以上を誇っていた。
2000年代に入り、電動アシスト自転車やノートパソコン、携帯電話(ガラケー)などの普及により、市場規模は5,000億円程度まで拡大し、と同時にリチウムイオン電池市場のシェア獲得に向けた争奪戦が繰り広げられることとなっていく。
当時はSANYO、ソニー、Panasonicの3社で世界シェアの60%強を占め、他の日本メーカー(NECトーキン、日立マクセルなど)を合わせると世界シェア90%を占めていた。
コンシューマ向け商品の普及に伴い日本企業各社は軒並み売上を伸ばしていったが、2000年代なかばから風向きが変わってくる。韓国LGやSamsungは日本品質の18650セル量産体制が確立され、リーマンショック後の円高などの影響もあり日本メーカーの競争力低下の隙をつき、2000年代終わりにはLGとSamsungで世界シェアの3割程度まで伸ばすこととなる。
2010年代は、スマホ市場の普及に加え電気自動車の期待が高まっていく。日産リーフや三菱i-Mievなど日本が世界に先駆けて電気自動車を市場投入し、大型ラミネート電池/角型電池での地位獲得を目指したが、インフラ面や技術面での課題解決が弱く市場拡大とはならなかった。
BYD、CATLの台頭
2010年代には、中国が国を挙げてリチウムイオン電池市場に本格的に参入することになる。リチウムイオン電池を積んだ電動バス向けに補助金を出し、上海や深圳、北京などの主要都市では2年間かけて電動バスに置き換えることに成功した。2020年には中国主要都市のタクシーをほぼEVに入れ替え、世界屈指のEV大国に成長する。
日本のリチウムイオン電池メーカーの現状
Teslaに電池を供給するPanasonicが日本のリーディングカンパニーとなり、村田製作所、TDK、東芝などが続いている。このPanasonicでさえも世界生産量は3位となっており、日本企業の世界シェアは減少の一途をたどっている。
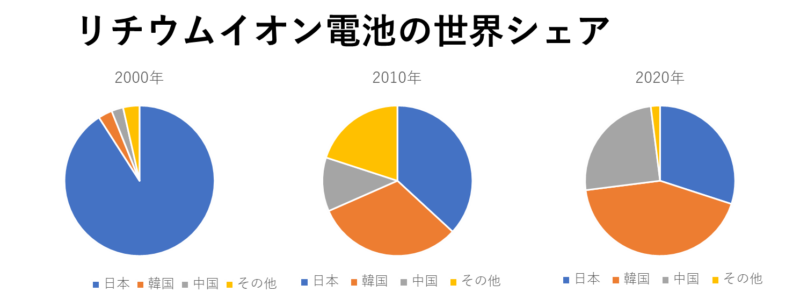
電池材料(正極、負極、電解液、セパレーター)
2010年代以降、日本の電池メーカーは電池材料のコスト課題に直面していた。1990年代~2000年代までリチウムイオン電池材料といえば、日本メーカーが支配しており、正極・負極製造における重要な焼成技術は日本メーカーが世界的に抜き出ていたためである。
ところが、欧州メーカーは品質/性能向上による市場拡大、中国はコスト競争力によりシェア拡大を進めることに成功した。2020年以降を見てみると、主要材料の生産は中国勢がトップとなり、日本メーカーは原材料費高騰などの影響を受け、苦戦を強いられている。
加速するEV化の流れ(2021年7月、EUが2035年以降のガソリン車販売禁止することがほぼ決定的に。)
2020年に入り、EV開発・競争により、CATLやLG、PanasonicなどのEV用電池の確保が過熱するなか、そのいずれの電池も日本国内で製造されることは無く、中国で製造するものが大多数を占めている。EVのキーデバイスである電池確保は自動車メーカーにとっては死活問題であり、残念ながら現在のEV用リチウムイオン電池の量産・価格競争力において日本国内で製造する事自体が既に破綻していることが大きな課題となり重くのしかかっている。つまり、現行のLIBにおけるEVビジネスを進めるにあたっては、自動車メーカーは中国や韓国からLIBを購入するしか手立てが無いのが現状である。
全固体電池の開発競争の始まり
全固体電池開発そのものは2000年代から始まっており、当初は安全性向上・エネルギー密度向上を目的として開発を行っていた。まずは固体電解質の開発を進める大学・企業が多く、常温における電気導電性の確保/Liの安定的な拡散などの課題解決に取り組み、2000年代後半に入ると界面の安定性などのテーマを進めることも増えてきた。
※当時は、うっかり八兵衛も全固体電池PJを進めていた経験もあり、固体電解質の動作電圧範囲や電池安全性を第一優先とすることから、LFP/LTOの組み合わせで取り組んだ経験もあるが、界面の課題・Liイオンの安定挙動(安定拡散温度)を克服できず断念している。
ところが、LIBのエネルギー密度の向上が10年間で200Wh/kgから280Wh~300Wh/kgとなり、開発目標のハードルが高まってくることに直面する。(自動車メーカーの重量エネルギー密度/体積エネルギー密度の要求が年々高まったことに起因する)
その結果、2022年の現在は全固体電池の開発として正極には硫黄系活物質がトレンドとなり、ハンドリングの厳しさ(水分に触れると硫化水素が発生する)を開発現場の研究員は体験していると思われる。
なぜ日本企業は全固体電池開発を推し進めるのか
・中国と韓国の台頭により、国内LIB事業は儲からず、既存LIBとは異なる電池事業が必要。
・自動車メーカーの電池部門内製化/国内安定調達の確保、海外依存の低下
・リチウムイオン電池/電池事業において世界シェアNo.1に返り咲きたい(国策)
・不安定な地金相場(コバルト、ニッケル、リチウム)の影響回避
さて、ようやく本題に入るのだが、全固体電池開発を必ず成功したい理由は上記3点に絞られる。リチウムイオン電池の主要4部材(正極、負極、電解液、セパレータ)の材料事業は、2010年まで順調に利益を出していたのは確かである。当時は正極・負極メーカーだけでも数十社あり、各社が性能最優先でしのぎを削っていたわけであるが、中国材料メーカーの品質向上・価格競争に飲み込まれてしまい、今は事業規模を変えずに戦っているのは10社程度まで減ってしまった。
これに待ったをかける動きが、NEDOやRISINGではプロジェクトで2030年の実用化を目指すプロジェクトが稼働している。また、文科省と経産省で連携して研究開発の情報交換のプラットフォームを構築し、今までにない産学官の取り組みを行っており、実用化に期待が高まっている。
ここまで資本投下する目的は、自動車産業と電池産業の覇権を握るために日本のプライドをかけていると思われる。
近年では半導体製造の国内回帰の動き、先進技術の海外流出を防ぐための対策も加速されており、国防の観点においても最重要戦略物質/部品と認定が進んでいる。
国策として進めている『革新型蓄電池実用化促進基盤技術開発』/RISING事業でのいち早い成功を期待するとともに、中国・韓国・欧州に流れてしまった電池事業の日本での復活を見てみたい。